Visible to Intel only — GUID: joc1463548749547
Ixiasoft
Visible to Intel only — GUID: joc1463548749547
Ixiasoft
PCB Design Guidelines for Channels with 25 Gbps + Interlaken Interface Connector Recommendations
P = 47.5 mil
L = 82.5 mil
W = 52.5 mil
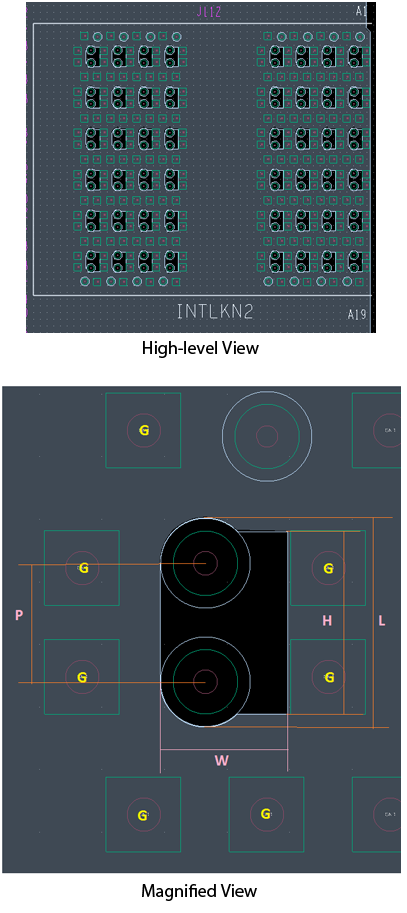
The maximum intra-pair skew (between P/N) is within 2 ps.
The GND reference cutout must be applied to all GND and reference planes. The dimensions of the GND cutout are 52.5 mil (W) x 72.5 mil (H).
The standard signal via used in Figure 100 has the following characteristics:
- 10 mil drill size diameter
- 26 mil pad diameter
- 36 mil anti-pad diameter
You must remove all non-functional pads.
Signal routing is differential on the main PCB before it reaches the Interlaken connector where it is turned into a single-ended routing.
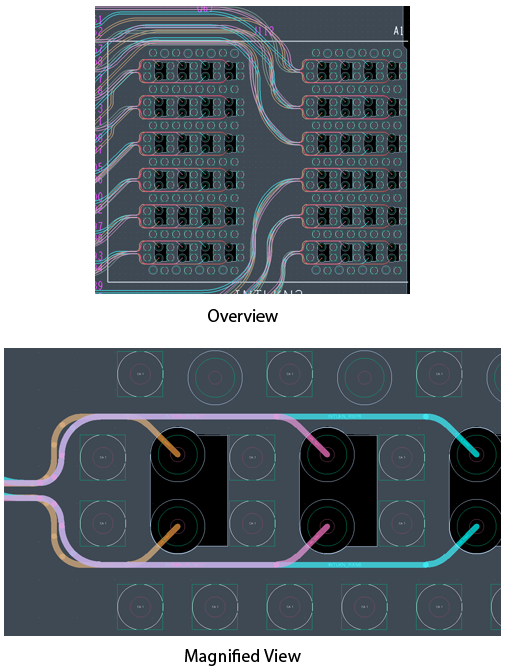
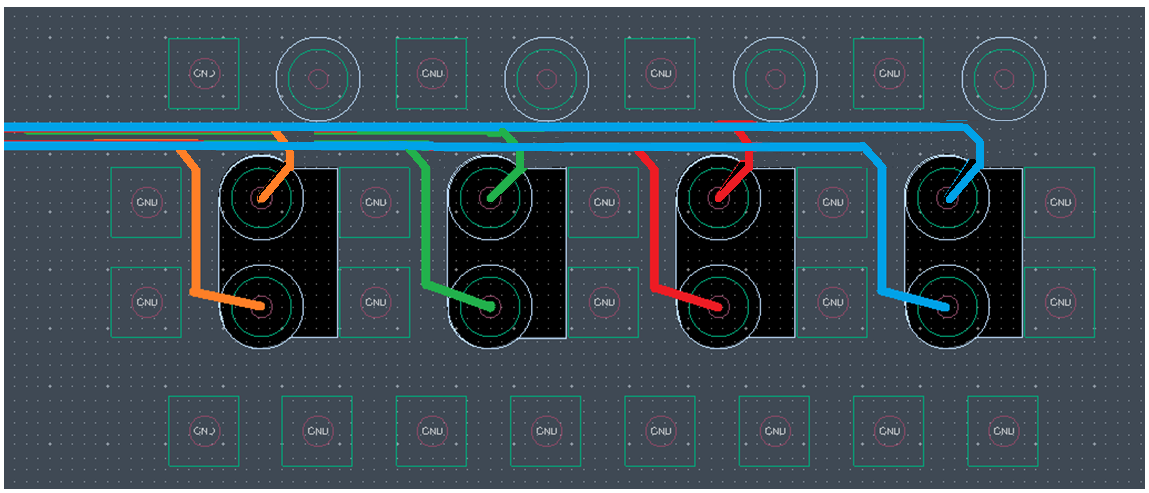
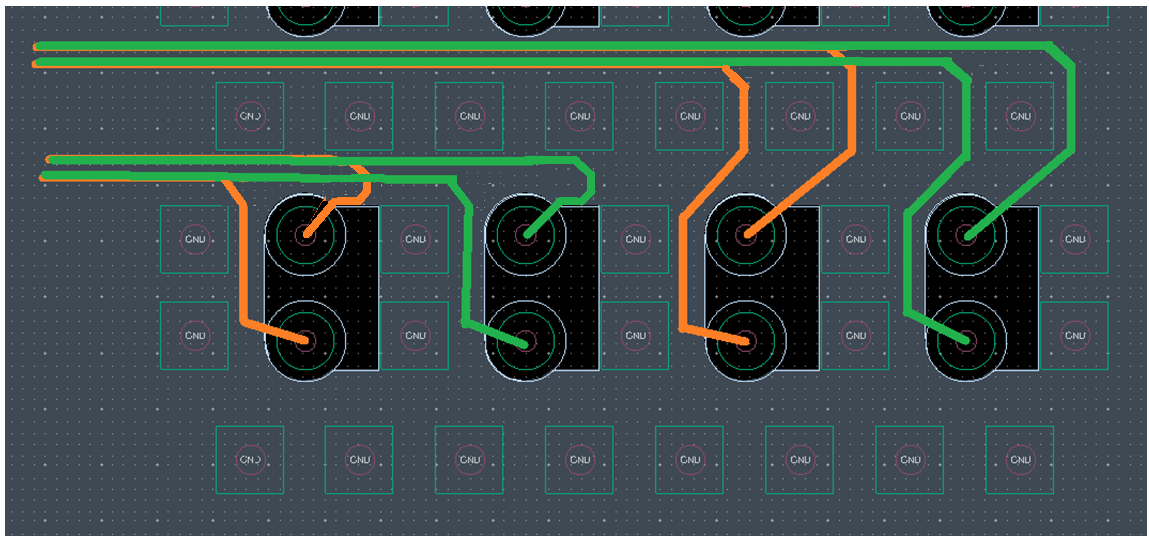
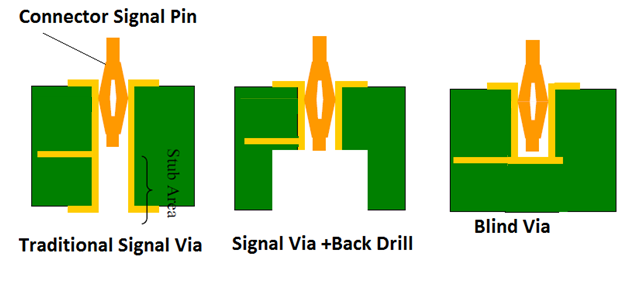
You can use either the signal via with back-drill, or a blind via at the Interlaken interface connector.
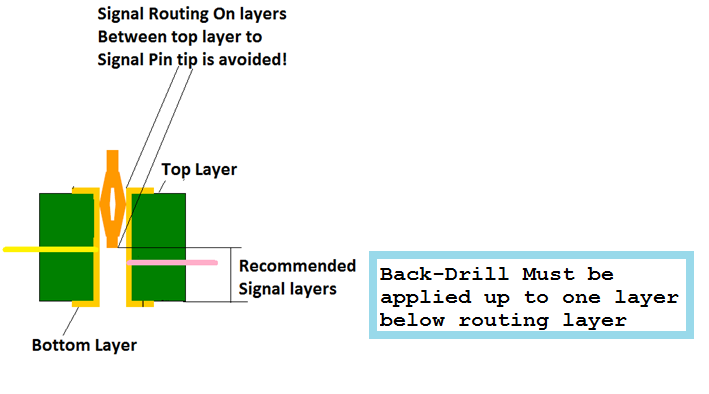
Signal routing is located on the bottom stack-up layer to minimize the impact of stubs in the channel. Observe the following recommendations for stack-up PCB design:
- Select the appropriate stack-up. Refer to PCB Stackup Selection Guideline chapter .
- Select the PCB routing layers:
- Separate TX and RX layers for maximum isolation
- The Interlaken interface connector pins have the following lengths:
- Connector GND pin = 1.88 mm
- Connector signal pin = 1.3 mm
- Use layers below the signal pin tip for all signal routing. This helps to avoid the stub from the connector pin if the upper layers are used for routing. Use either the signal through via with back-drill or the blind via.
- Intel recommends using a 95 Ω routing trace impedance because it aligns with the following guidelines:
- For FPGA break-out, refer to FPGA Fan-out Region chapter.
- Use a 100 Ω loosely differential routing on the main host PCB if you are using option 1 in Figure 101 at the connector.
- Use a 100 Ω tightly differential routing on the main host PCB up to the connector pins if you are using option 2 in Figure 102 at the connector.
- Use the smallest routing length possible to minimize insertion loss and crosstalk.
- Ensure that all RX paths have an AC capacitor for AC coupling. Refer to the AC coupling layout design guideline in AC Coupling Capacitor Layout and Optimization Guidelines chapter.
- Ensure that you have length matching (less than 2 ps) for all TX and RX paths if this is a requirement. Refer to Recommendations for High Speed Signal PCB Routing chapter for length matching strategies at the FPGA.
- Use a back-drill for all transceiver signal vias if a through via is used.