Visible to Intel only — Ixiasoft
Visible to Intel only — Ixiasoft
This routing design is configured with the following characteristics:
- The stack-up is 24 layers with a thickness of 117 mil
- Eight signal layers
- Four PWR layers
- Material is Megtron6
- Via-in-pad topology with 8 mil finished drill
- 18-mil signal pad and 28 mil signal anti-pad
- Horizontal anti-pad is 68 mil (40 mil pitch + 28 mil anti-pad)
- Vertical anti-pad is 28 mil
The transceiver pair of A and B have been routed on the layer 5 of stackup. Transceiver pair of C and D on the same row have been routed on a different layer. Only two signal layers are required for four transceiver pairs by using conventional differential routing with neck-down and jog-out routing.

Yellow routing shows transceiver pair A routed on layer seven. Red routing shows transceiver pair B routed on layer nine. Due to single-ended break-out and lack of space, the transceiver pairs C and D on the same row have been routed on different layers. Four signal layers are required for four transceiver pairs by using conventional single-ended in-line breakout routing with jog-out.
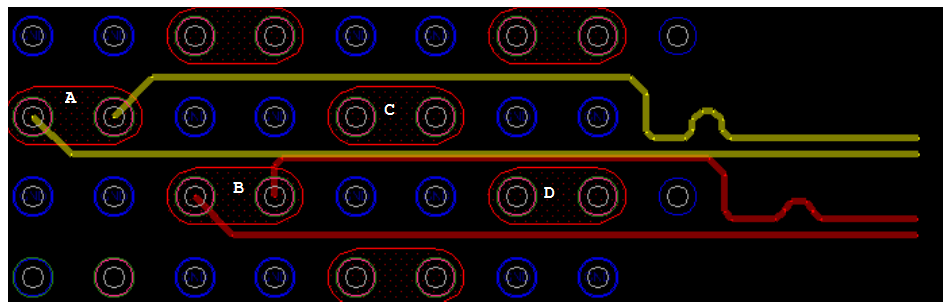
Because fabrication always has some layer-to-layer mismatch, this example implements a typical 5 mil layer-to-layer mismatch to the cases above. This allows you to observe the level of sensitivity to layer-to-layer fabrication mismatch. This layer-to-layer fabrication mismatch moves the routing passing by the GND void area and adds more discontinuity to the routing path.
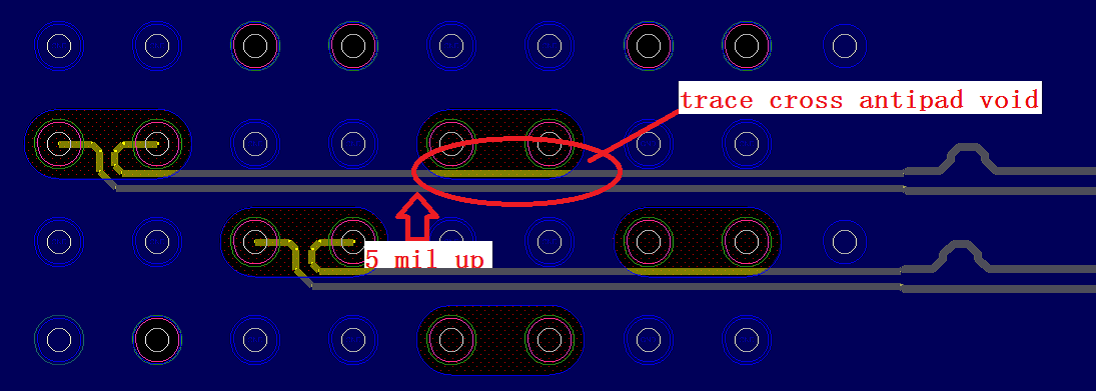

Performance Comparison Between Case 1 and Case 3
This section compares the performances between conventional differential routing with neck-down and jog-out with/without mismatch (Case 1 vs Case 3).


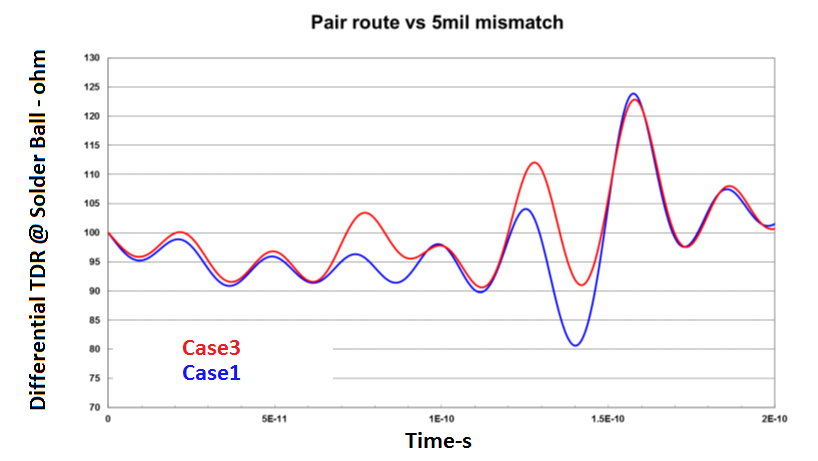
These performance results demonstrate that within 15 GHz bandwidth Case1 is robust enough to accommodate the layer-to-layer fabrication mismatch. The TDR impedance shows up to 7 Ω impedance mismatch due to the 5 mil layer-to-layer mismatch.
Performance Comparison Between Case 2 and Case 4
This section compares the performances between conventional single-ended in-line routing with jog-out with/without mismatch (Case 2 vs Case 4).
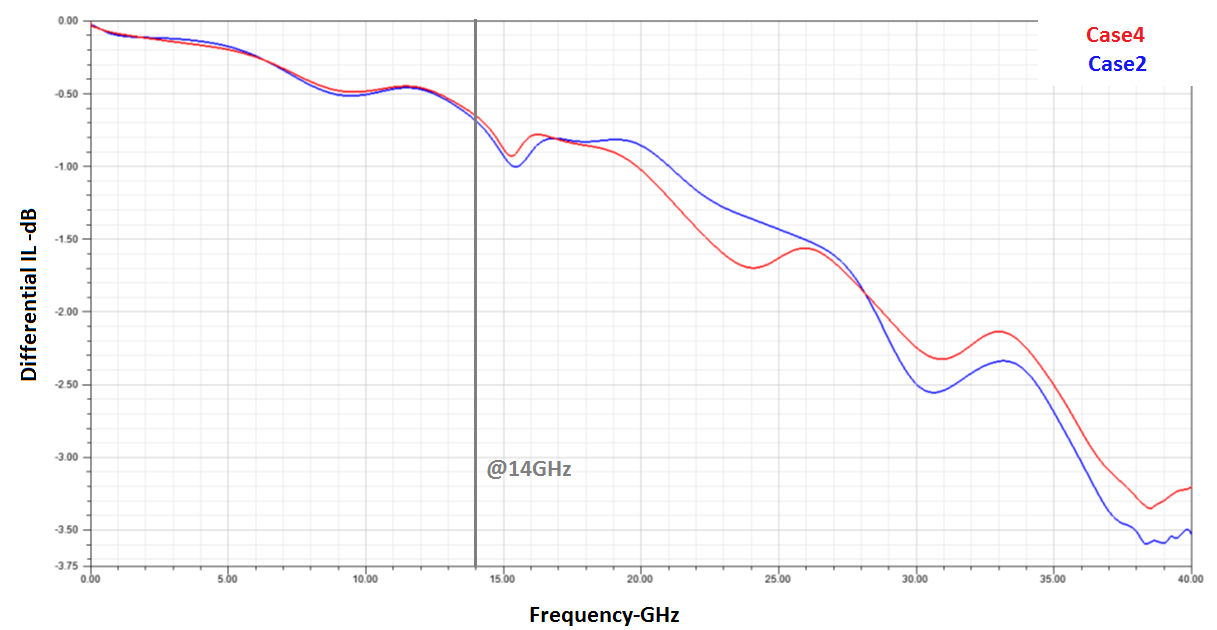

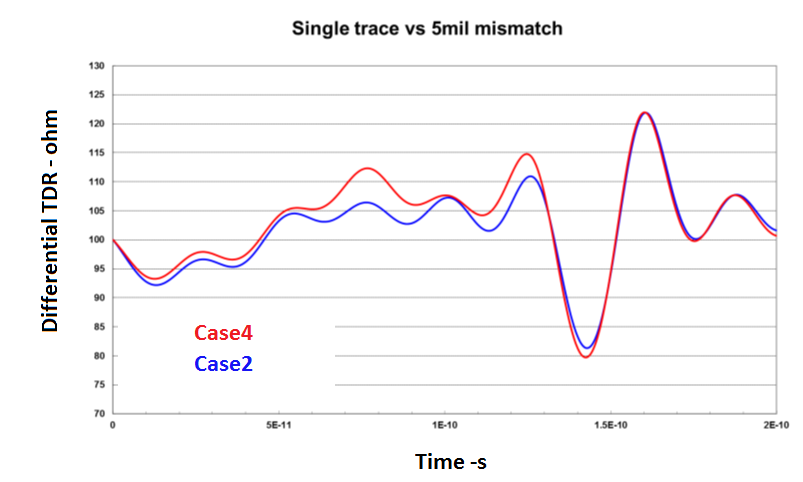
These performance results demonstrate that within 15 GHz bandwidth, Case 2 has a more robust layer-to-layer fabrication mismatch. The TDR impedance shows up to a 5Ω impedance mismatch occurring due to the 5 mil layer-to-layer mismatch.
Intel recommends that the break-out routing is either differential neck-down with back-jog or single-ended bak-jog routings due to the fixed skew matching at the BGA area. The following figures demonstrate the recommended break-out routing performances.


Performance Comparison Between Case 1 and Case 5
This section compares the performances between conventional differential routing with neck-down and jog-out and differential routing with neck-down with back-jog (Case 1 vs Case 5).


Comparing the conventional differential and jog-out routing configurations with the recommended differential routing with back-jog shows up to 0.1 dB insertion loss improvement. It also exhibits up to a 5 dB return loss improvement within a 15 GHz bandwidth when using the back-jog configuration.
Performance Comparison Between Case 2 and Case 6
This section compares the performances between conventional single-ended in-line breakout routing with jog-out and single-ended routing with back-jog (Case 2 vs Case 6).

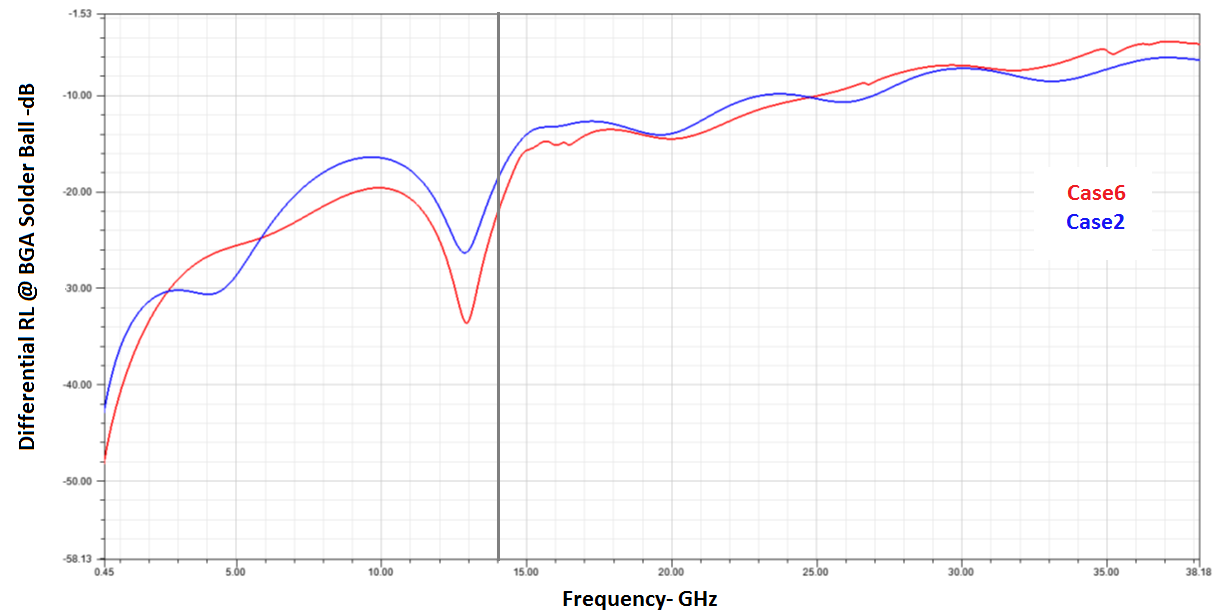
Single-ended break-out routing is less sensitive to layer to layer mismatch.
Comparing the conventional single-ended routing with jog-out and the recommended single-ended routing with back-jog, the single-ended routing with back-jog shows an insertion loss improvement of up to 0.25 dB. It also exhibits a return loss improvement up to 7 dB within a 1 -GHz bandwidth.
The differential break-out routing with back-jog shows 0.1 db insertion loss improvement and up to 6 dB return loss improvement within 15 GHz bandwidth compared to single-ended break-out routing with back-jog.
In addition, differential break-out routing with back-jog has slightly better performances above 15 GHz compared to single-ended routing with back-jog.
Intel recommends use of single-ended routing with back-jog due to less sensitivity over the layer-layer mismatch, if customers use low number of transceiver channels or they have enough signal layers for routing. Due to this, differential break-out routing with back-jog is preferred to single-ended break-out routing with back-jog, because differential break-out routing requires half of routing layers used for single-ended break-out routing.