6.6. CFD Model
The following figure shows the CFD model for this example, where the PCIe card occupies two slots, about 40 mm wide for the face bracket. Airflow to the slot is 15 CFM at 50°C.
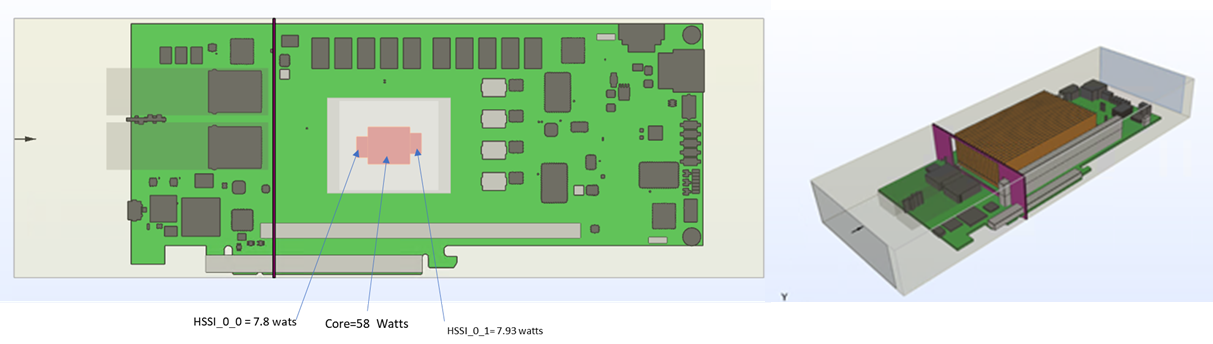
CFD Results
This cooling solution would be viable if the TCASE were equal to or less than 88.2°C; however, the CFD result for TCASE is 86.8°C, as shown below.
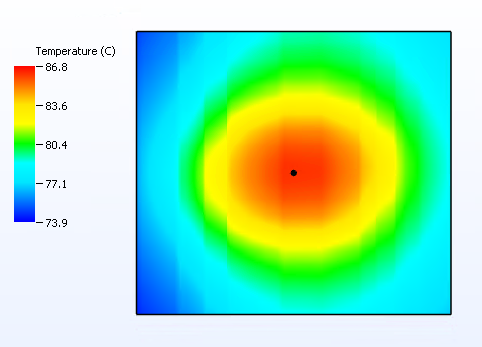
Consequently, the TJ temperatures are less than the TJ limit entered in the Intel® FPGA Power and Thermal Calculator (PTC), and the cooling solution is viable. When the temperatures are close, you can assume a linear relationship in estimating the maximum junction temperatures. So, in this case, the maximum TJ is ~88.2-86.8= 1.4°C less than the 95°C limit set in the PTC. However, the lower temperatures cause power consumption to go down, and temperatures to drop further.
CTM Case Temperature Sensor
Not all the CTMs provided have a built-in temperature sensor at the center of their integrated heat spreader (IHS). If the CTM for your project does not have a built-in temperature sensor at the center of the IHS, Intel recommends that you add one. You should place the temperature sensor at the top center of the IHS and ensure that it does not touch the heat sink.