Innovate from Edge to Cloud in Industrial Automation with Intel® FPGAs
With Intel FPGAs, industries are enabled to develop safe, reliable and optimized designs.
Solving Industry Challenges with Intel® FPGAs
Intel delivers solutions enabling innovation from edge to cloud in industrial automation. With Intel® FPGAs, industries are enabled to develop safe, reliable, and optimized designs. Intel provides a wide range of FPGAs and ARM core integrated SoC devices, tools, IPs, reference solutions, etc., catering to diverse application use cases, including artificial intelligence, edge computing, and robotics.
Smart Energy
The use of FPGAs in smart energy applications brings benefits such as improved performance, flexibility, real-time processing, energy efficiency, integration capabilities, scalability, and enhanced security. These advantages contribute to the development of efficient, reliable, and intelligent energy systems that can support sustainable and optimized energy generation, distribution, and consumption.
As transportation vehicles are electrified, attention switches from fuel consumption to electrical energy consumption and the efficiency and cost of power converters. DC Fast Charging (DCFC) technology is used in level 3 EV charging stations where the charging happens fully within the station, and it uses DC power, allowing users to charge an EV in as little as 30 minutes fully.
FPGAs are unique in enabling custom digital control at very high frequencies. They are beneficial in reducing the size and cost of passive components and minimizing the power lost in AC/DC power conversion.
FPGAs also support battery management. Unlike charging with AC power, DC fast charging risks overloading EV batteries, which could contribute to their decay or loss of range over time. FPGAs support batteries and BMS by providing the compute necessary to evenly distribute loads across cells, eliminating the threat of decay and providing greater longevity to the battery.
Read the Electric Vehicle (EV) Charging eBook ›
Watch the video on EV charging solutions from Intel and Imagen Energy ›
See the Three-Phase Boost Bi-directional AC/DC Converter design example ›
Producing reliable, more efficient, and less costly solar or photovoltaic (PV) systems is important in making solar energy more competitive. This poses challenges in designing the solar inverter architecture to meet the following demands:
- Reliability and long service life to supply distributed renewable energy sources with central power generation for growing power needs.
- Increased efficiency and lower unit costs using advanced control algorithms and power topologies like 3-level insulated gate bipolar transistor (IGBT) and wide-bandgap SiC-FETs.
- Local grid code compliance, which includes power quality monitoring and control.
In the past, traditional PV inverter architectures consisted of a DSP for maximum power point tracking (MPPT) and DC-DC control, an FPGA for the DC-AC control, and perhaps a separate MCU to handle system communications. These three separate system components can be aggregated into an Intel® FPGA by integrating the DSP control loop, DC-DC, and DC-AC conversion and communications all on a single device.
Distributing electric power and managing power grids are undergoing transformation and have become the focus of new technology approaches for several reasons:
Aging equipment.
Distributed energy resources (DER) contribute to grid instability, for example, due to the growing number of solar panels feeding electricity back to the grid and charging electric vehicles in their garages.
Local grid code compliance, which includes power quality monitoring and control.
Utilities looking for reliability; Capex/Opex reduction and real-estate cost savings.
Equipment standardization by utilities to avoid vendor lock-in.
Intel FPGAs are ideal for a newly transforming power grid. They satisfy the real-switching requirements in a redundant network. Our Intel FPGAs meet Gbps ethernet traffic performance requirements with HSR/PRP redundancy and evolving HSR/PRP standards.
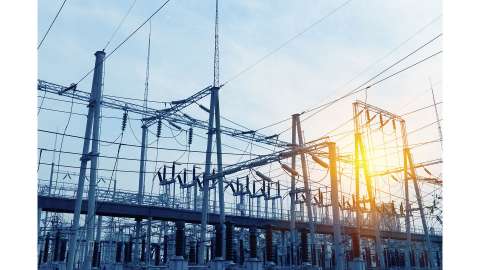
Getting Started
Three-Phase Boost Bi-directional AC/DC Converter
This design example demonstrates an implementation of a three-phase boost bidirectional AC/DC converter for EV charging. MAX® 10 and Cyclone® V SoC FPGA Development Kits are the target devices for this reference design.
MAX® 10 DC-DC Converter
The design example demonstrates a digital controller that can control a Hybrid DC-DC Converter with variable voltage control (VVC). The design uses DSP Builder for Intel FPGAs (Advanced Blockset) to simulate and synthesize VHDL control. The design targets the Intel MAX 10 FPGA Development Board.
FRS (Flexibilis Redundant Switch)
FRS is an IP core providing HSR / PRP functionality, which supports 3–8 port layer 2 switch in triple speed (1Mbps / 10Mbps / 1Gbps). You can access to evaluation kit, user manual, and reference designs from TTTech.
White Papers
Robotics
FPGAs bring benefits to robotic applications such as low latency, functional safety, deterministic compute, connectivity, and more. They support static and mobile robots such as AMRs, AGVs, and 6-axis robot arm. We provide several robotic solutions.
Robots are becoming more and more prevalent in the industrial workplace. Super high-speed industrial robots handle difficult and hazardous tasks like assemblies, welds, and pick-and-place. Collaborative robots, or cobots, work hand-in-hand with humans, requiring a functionally safe environment. Autonomous Mobile Robots (AMRs), many vision–guided, function individually and in cloud-control swarms.
Intel FPGAs provide the needs for industrial robots through:
- Deterministic computing: Brings precision and multi-axis motor control benefits to robotics, significantly lowering the cost of bill-of-materials and reducing latency to improve accuracy.
- Connectivity: Time-sensitive networking (TSN) coordinates the multiple axes of a single robot and between multiple robots.
- Functional Safety: Intel Functional Safety Data Package (FSDP) and TÜV Rheinland-certified CAT3 PLD Safety Concept provide FuSa functionality and accelerate time-to-market by compressing certification cycles for customers.
Together with Intel® FPGA Video and Vision Processing IP Suite, OpenVino™ toolkit, and Intel® FPGA AI Suite, you can deploy vision functionality beyond color and shape inspection, such as safety hazard detection and object recognition/classification.
Yaskawa: Intel® FPGA in Robot Controllers
Yaskawa implements Intel® FPGAs in its high-performance robot controllers for servo control and functional safety.
Veo Robotics: FreeMove 3D Safeguarding System
Veo Robotics use Intel® FPGAs to enable its Veo FreeMove* 3D safeguarding system for flexible human-robot collaboration.
Getting Started
Agilex® 7 FPGA Drive-on-Chip Design Example
The Intel drive-on-a-chip motor control reference design is an integrated drive system on an Agilex® 7 device. The design demonstrates synchronous control of up to two three-phase permanent magnet synchronous motors (PMSMs) or brushless DC (BLDC) motors. You can adapt the design to other motor types.
Cyclone® V and MAX® 10 FPGAs Drive-on-Chip Design Example
The Intel drive-on-a-chip motor control reference design is an integrated drive system on a single Cyclone V SoC or MAX 10. The design implements single- and multi-axis field-oriented control (FOC) supporting concurrent control of up to four permanent magnet synchronous motors.
Machine Vision and AI
FPGA enables direct ingest of data, pipelined image processing and AI implementation with deterministic and low latency.
Machine vision technology is rapidly evolving for higher image resolution, higher frame rate, adoption of new interfaces and adoption of AI.
Cameras and other equipment used in machine vision perform a variety of different tasks, such as Image Signal Processing (ISP), video transport, format conversion, and analytics. Because of the frequent technology improvements to camera sensors, the advancement of artificial learning and deep learning-based video analytics, Intel® FPGAs play a key role in next-generation Machine vision cameras, frame grabbers, and vision controllers:
- Flexibility to interface to many types of image sensors and MV system devices.
- Fast processing to incorporate a full image sensor pipeline (ISP) that includes techniques, such as defect pixel correction, gamma correction, dynamic range correction, and noise reduction.
- Support for AI deep learning frameworks, models, and topologies to implement FPGA-based convolutional neural network (CNN) inferencing accelerators.
Learn more about Intel® FPGA AI Suite ›
Learn more about the Intel® FPGA Video and Vision Processing IP Suite ›
Hamamatsu Photonics: High-Performance Industrial Cameras
Hamamatsu selected Arria® 10 and Cyclone® 10 FPGAs for high-performance ORCA-Quest* scientific cameras and new X-ray food inspection systems due to their real-time image-processing capabilities and high-bandwidth interfaces.
Critical Link LLC: MityCAM
Critical Link LLC integrates Intel® FPGA AI Suite into its MityCAM Camera evaluation kit for the Canon 5MP image sensor with USB3 Vision interface. It also uses Arria® SoC FPGA to perform object detection, image processing workloads, and sensor/display interface all in one chip.
Getting Started with Image Signal Processing (ISP) Design Example
Create your advanced camera products with a collection of Intel® FPGA IP cores. With customized real-time, low latency image and video processing, and ease of use with rich programming interfaces (APIs) and standard interfaces, these IP cores allow a plug-and-play process that accelerates your ISP product time to market.
Log into your intel.com account to download the design example › or
Smart Manufacturing
FPGAs enable the seamless integration of various components and systems, such as sensors, actuators, and machine learning algorithms, facilitating intelligent decision-making, predictive maintenance, and adaptive control in smart manufacturing environments.
Motors and drives power countless industrial processes in production, assembly, packaging, robotics, computer numerical control (CNC), machine tools, pumps, and industrial fans. These motor-driven systems account for more than two-thirds of industrial energy consumption, making their efficient operations vital to factory profits.
Designing motor control and motion control systems with Intel® FPGAs and SoC FPGAs can result in significant reduction in overall cost of ownership through:
- System Integration: Lower Bill of Materials (BOM), power consumption, and reliability challenges by integrating industrial networking, functional safety, encoder, and power stage interfaces and digital signal processing (DSP) control algorithms in a single device.
- Scalable Performance: Use a single scalable platform across entire product lines. Achieve higher performance with faster and more advanced deterministic control loops.
- Functional Safety: Reduce compliance time and effort with devices and tools that meet Machinery Directive IEC61508 safety standards.
Programmable Logic Controller (PLC) is an industrial computer used for controlling the automation of industrial processes. PLC is a computer-based solid-state device that is designed to withstand harsh factory conditions and carry out real-time monitoring and control of different industrial processes.
PLCs are used extensively in almost all industrial processes, but current systems are typically optimized for a specific domain as a closed system. As Industry 4.0 drives further automation across multiple domains over the network, PLCs are getting integrated into larger computing platforms (like edge computers) as a software function to enable workload consolidation.
FPGAs are commonly used for I/O expansion, industrial Ethernet, and field bus communication devices to enable deterministic, low-latency parallel computing of PLC. Also, FPGA is used for functional safety as some PLCs are used for safety-critical applications. Intel and its partners offer a variety of IP cores as well as safety certified SKUs and Functional Safety Data Package.
TSN solution from Intel and TTTech
IEEE 802.1 TSN allows the mixing and matching of industrial hardware and software solutions from different vendors providing real-time deterministic connectivity.
Intel and TTTech Industrial Automation AG provide an out-of-the-box solution with no up-front license fees, no per-unit royalty reporting, and no protracted negotiations.
TTTech TSN IP solution for Intel® FPGA supports:
3/5 port 10/100/1000 Mbit/s switched endpoint
IEEE 802.1 AS, IEEE 802.1 CB, Qbv, Qbu, Qcc
Linux* kernel 4.14 LTS
- Cut-through and store and forward
Industrial Ethernet Solutions with Intel and Softing
Intel® FPGA-based Industrial provides the connectivity for seamless integration of legacy industrial Ethernet.
To make it easier to add industrial Ethernet to your design, Intel and Softing Industrial Automation GmbH provide an out-of-the-box solution with no up-front license fees, no per-unit royalty reporting, and no protracted negotiations.
This solution contains Profibus, Profinet, EtherCAT, EtherNet/IP, and Modbus protocol. Licensing is tracked using an external Security CPLD that unlocks the protocol IP loaded into the FPGA at boot time.
Exor Embedded SoM (System on Module)
Exor provides Intel® FPGA-based production deployable SoMs and RRKs for TSN and brownfield protocols that are already proven-in-use for manufacturing use cases with robust quality and long lifecycle support.
ISO 13849-1 Cat. 3 PLd
Our Technical Safety Concept describes how to achieve a Cat. 3 PL d equivalent risk reduction according to ISO 13849-1 and IEC 61508 SIL 2, reviewed and approved by TÜV Rheinland. It demonstrates a possible implementation of a system based on an Intel® SoC FPGA, using the example of a Cyclone® V SoC FPGA and an external safety logic (ESL) device for industrial process automation and machinery safety application.
Functional Safety Data Package (FSDP)
Using the certification of tools and devices and the guidance in our certified Safety Integrity Level 3 (SIL3) Functional Safety Data Package, developers can shorten IEC 61508 development time and reduce certification risks across many safety-critical industrial applications.
In addition, the Safety Separation Design Flow retains the FPGA benefit of quick upgrades/bug fixes while reducing the need for full design recertification.
SafeFlex Safety Reference Board from NewTec
To further reduce customer design effort in safety designs requiring IEC 61508 certification up to SIL3 and IEC 13849 PLe Cat 4, Intel and NewTec have partnered to develop the SafeFlex functional safety reference board.
Empowering Semiconductor Manufacturing Equipment with FPGAs
This white paper proposes integrating Intel FPGAs within mask writers and surface inspection tools to improve machine performance and, thus, assist foundries worldwide in meeting chip demand.
Flex: Intel® FPGAs in Smart Factory
This white paper explains an innovative approach Flex took to achieve Industry 4.0 transformation for its Surface-Mount Technology (SMT) line based on Intel® FPGAs.
V-Sync: Smart Vending Motor Control by V-Sync
V-Sync implements motor control of 12 I2C ports in their smart vending machines by using an Intel® FPGA that offers real-time responsiveness and control features.
Solution Briefs
White Papers
Industrial Connectivity
Functional Safety
Videos
Browse Intel and Partner Solutions
Take advantage of ready-to-deploy solutions from Intel and our partner ecosystem to accelerate your projects.